職業健康及員工安全
本公司除有廠區門禁保全措施外,對於工作場所之通道、地板、通風、照明、作業區、機械設備與防火防災…等,提供員工符合法令規範的作業環境,事故通報、調查及記錄皆於公司內部訂定之”職業安全衛生工作守則”中載明。本公司之工作環境與員工人身安全保護措施彙整如下:
一、進出管制:
1. 本公司由委託之保全公司實施門禁管理,加強人員、車輛及物品出入公司之管制,所有訪客及進出貨皆需換證登記並配戴識別證,進入廠區員工需刷卡,以確保廠區安全及管理。
2. 生產現場、實驗室及原、物料場所另設權限管控,依廠內生產區域人員進出管理之規定管理。
二、各項設備之維護:
1. 本公司之設備系統,包含空調、高低壓電氣設備、運輸、機械、消防器具、水及氣體等系統,由責任單位共同研擬並依計劃實施,機械設備之使用單位(或責任單位)必須依照法令規範實施定期檢查、維護與保養。
2. 對列管之危險性機械、設備(如:固定式起重機、堆高機…等),依職業安全衛生相關法令,每年進行定期檢查,於使用合格證到期前,向職安署委託之合格代檢機構,申請進行機械設備之定檢,檢查合格並取得使用合格證。
三、災害防範措施:
1. 訂有「T-SSHD-007 緊急應變管理程序書」、「T-SSHS-031 安全衛生工作守則」、「T-SSHS-002 作業安全暨環境安全作業標準」、「T-SSHS-004 作業區域6S規範」等災害防止、搶救注意事項及事故職災通報程序,明確規範本公司各級人員對突發狀況事前及事後應負責任及任務內容。
2. 為維護員工安全與衛生,推展安全衛生業務,編制職業安全衛生業務主管三人及職業安全衛生管理員一人,並向轄區主管機關報備。
3. 對於廠內從事危害性化學品相關作業人員,實施危害通識教育訓練,以提升作業人員正確的安全衛生觀念,讓作業者在使用、貯存危害性化學品時依規範採取適當措施。
4. 在製程設備操作及化學品使用時,提供相關安全防護器具,例如護目鏡、耐酸鹼手套、安全帽、安全鞋,避免發生危害;於現場放置緊急應變器材,可供異常發生時,能夠及時處理,降低災害發生之嚴重性及範圍;定期實施作業檢點。
5. 在具有顯著噪音環境作業時,首先評估工程減噪,若不可行或有執行困難時,提供該作業區員工聽力防護具(如耳塞、耳罩)配戴之。
6. 擔任危險性機械、設備之操作人員須取得合格證照,每月進行檢查及維護保養,每年進行定期檢查,由政府委辦機構進行廠內定期之檢查。
7. 工程發包於承攬廠商進廠施作前,施以安全衛生教訓練及危害告知(若有再承攬商則由總包廠商實施安全衛生教育訓練),確實讓承攬廠商知悉施工現場之環境危害及需注意之安全事項,承攬廠商派監工確實監督現場之安全管理,本公司工安單位不定期至現場稽核作業狀況。
四、消防安全管理:
1. 依法規定設置之消防系統,包含警報系統、消防水系統、逃生系統及防火管理員...等,由防火管理員統籌相關消防事項。
2. 為落實消防安全設備之維護管理,依消防法規定,每年11~12月委託消防設備師/士或專業檢修機構檢修廠內消防安全設備,並於檢修完成後十五日內,依規定將檢修結果報請當地消防機關備查。
3. 本公司定期進行消防演練,從事工作所必須之安全衛生教育及防災相關訓練及在辦公室及廠房內均設置有緊急逃生路線及出口演練。為落實平時之火災預防作為,依場所之使用特性、防火避難設施、燃氣設備及消防安全設備之設置等情形,消防管理編組為滅火班、安全防護班、通報班、避難引導班、緊急救護班,廠內人員皆須負起火災防制之責任。
五、生理與心理安衛措施:
1. 健康檢查:新進人員到職前需做體格檢查,在職人員依據職業安全衛生法相關要求,依法令規範定期實施健康檢查及特殊作業健康檢查。
2. 工作環境衛生除已規劃設置之吸菸區外,全廠區禁止吸菸及嚼食檳榔,並定期進行廠區環境清潔及消毒。
3. 訂定並執行人因傷害預防、女性勞工母姓健康保護、異常工作負荷促發疾病預防計畫、職務遭受不法侵害預防辦法,預防與照顧員工身心健康。
4. 員工意見表達:設立員工意見投遞信箱,由管理部統一受理讓員工意見表達、情緒宣洩等,亦可強化員工與公司間的互動。
5. 性騷擾防治:為防治工作場所性騷擾,訂定工作場所性騷擾防治措施申訴及懲戒辦法,以維護及創造安全之工作環境。
六、實施自動檢查:
1. 各單位依照作業內容進行機械、設備之自動檢查,自動檢查內容與表格依實際情形增減編訂,但法令強制規定之檢查內容不得刪除。
2. 實施作業前、中、後檢點。於作業前進行檢點,在掌握環境因素、機械設備及作業特性;作業中之檢點可避免掌握現有安全狀態,是否因不可預知或人為因素,造成現有安全設施之故障;作業後之檢點,可進行工作上之交接及傳達作業場 所之現狀情形。
3. 危險性機械、設備定期(日/月/年檢)檢查及維護保養,由政府主管機關委辦機構進行廠內設備之檢查,並配合檢查人員適時將設備汰換或改善,經通過檢查取得合格使用證照後,現場人員方能使用。
七、作業環境監測:
目的為了解作業場所存在之危害因子及其可能對作業人員健康之影響。
本公司實施作業環境監測前進行下列步驟:
1. 擬定含採樣策略之作業環境測定計劃,從基本資料蒐集、原物料、製程流程、危害物清查開始進行,並透過觀察、訪談記錄、調查的方式,規劃相似暴露群,然後,再針對最大可能暴露者實施採樣。
2. 確認監測項目及位置,包含二氧化碳(CO2)、照度、噪音、有機溶劑……等。
八、化學品管理:
依據危害性化學品標示及通識規則,進行以下化學品管理事項:
1. 安全資料表(SDS) 置於現場人員易取得之處。
2. 安全資料表至少每三年更新一次,並留存更新記錄。
3. 於容器、桶槽或儲存場所,張貼明顯標示。
4. 製備危害性化學品清單。
5. 對相關作業人員施行化學品危害通識之教育訓練。
6. 定期執行優先管理化學品申報。
九、教育訓練:
1. 員工必須參與安全衛生教育訓練,訓練時數依法規規定。
2. 從事職業安全衛生工作人員,應依職業安全衛生教育訓練規則,取得相關證照並定期接受複訓。
3. 從事危險性機械、設備及特殊作業之人員,視作業條件接受外部合格之訓練機構教育訓練取得訓練時數或合格證照。
十、職災預防:
1. 每季招開在職同仁職業安全衛生相關教育訓練,以提升同仁安全意識及觀念,以降低職災發生率。
2. 針對廠內發生職災之事件進行事故追蹤單檢討,並依事故追蹤單要求請發生事故單位主管提出針對事故之改善對策及預防再發措施進行檢討簽核。
3. 每月針對巡查發現安全缺失單位開立巡查缺失改善單,並於次月針對缺失人員招開工安講習課程,加強及提升人員安全意識。
4. 工傷零容忍,目標設定廠內零職災。
十一、本公司於2024年12月12日取得ISO 45001職業安全衛生管理系統,驗證合格通過。
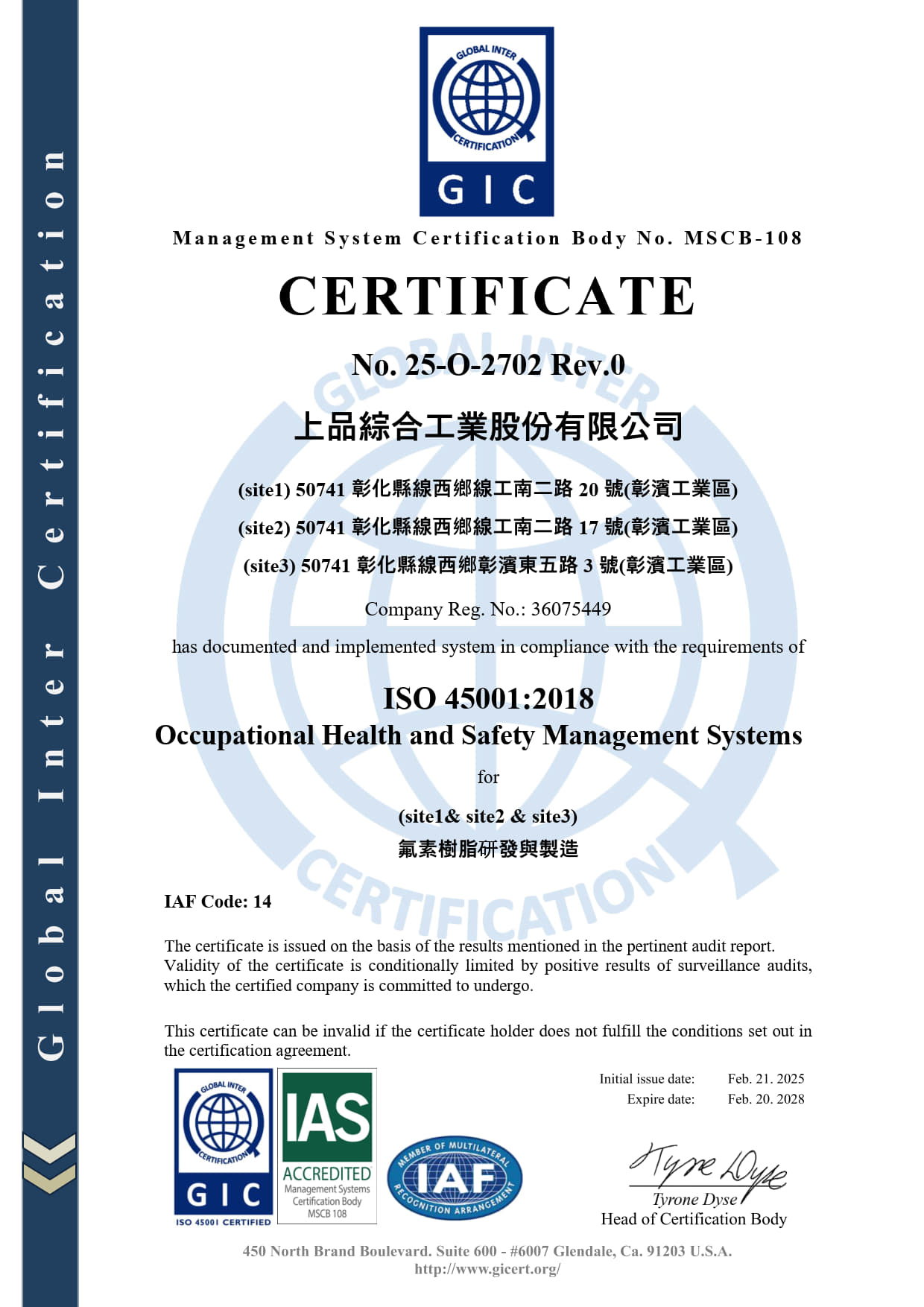
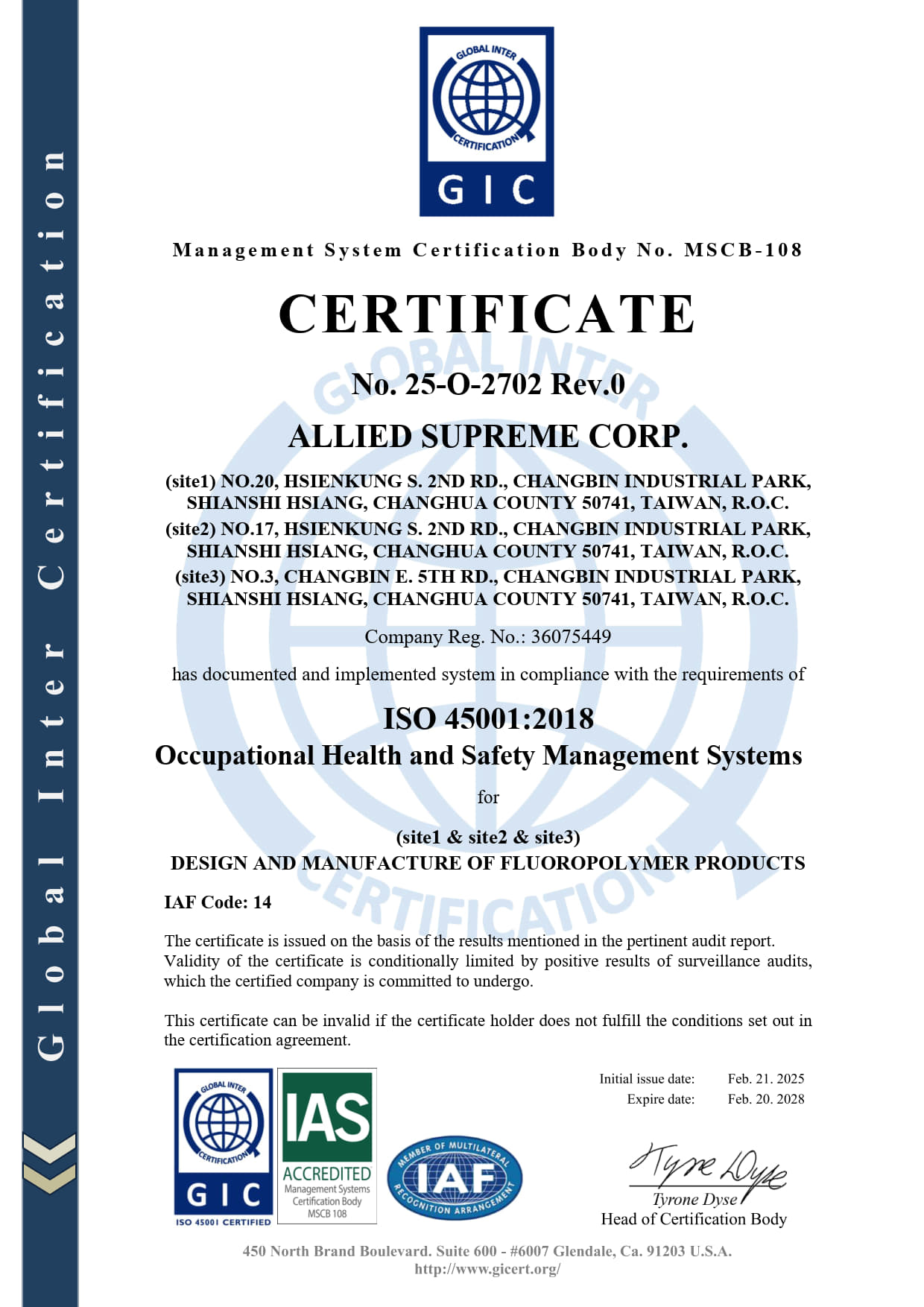